Quality Welding Supplies: Your Essential Guide to Tools and Equipment
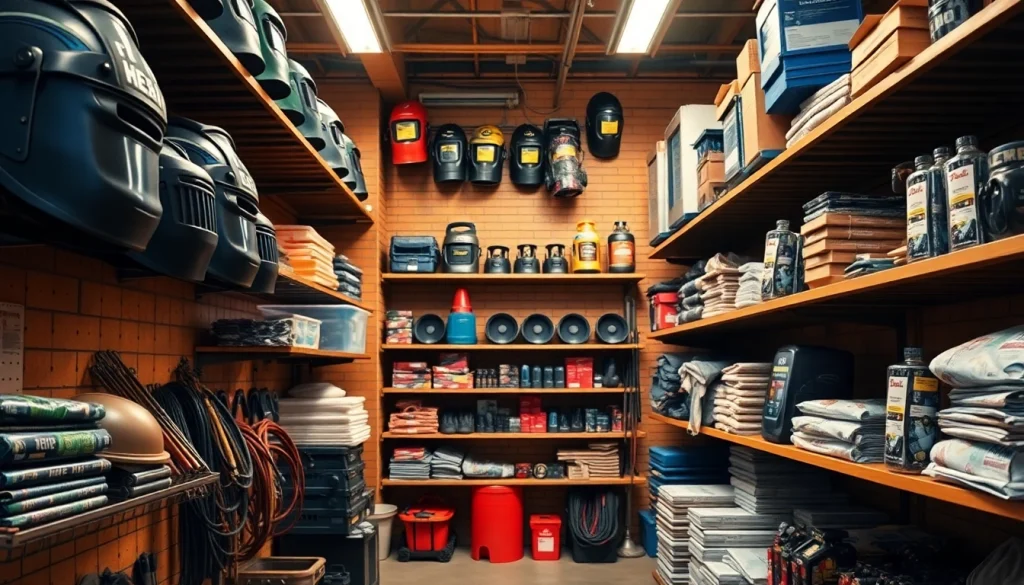
Introduction to Welding Supplies
Welding is a fundamental process in various industries, including construction, automotive, and manufacturing. Essential to this process are welding supplies that ensure welders have the right tools and materials at their disposal. From electrodes to protective gear, understanding the scope and significance of welding supplies can enhance the quality of work and ensure safety on the job. This guide covers the critical components of welding supplies, their importance, and how to choose and maintain quality equipment.
What are Welding Supplies?
Welding supplies encompass the various tools, materials, and equipment required to perform welding tasks effectively. This includes welding machines, consumables like electrodes and filler materials, safety gear, and accessories to enhance the welding process. Each type of welding—be it MIG, TIG, or Stick welding—necessitates specific supplies tailored to optimize performance and meet industry standards.
Types of Welding Supplies
Welding supplies can be categorized into several key types:
- Welding Machines: Essential for any welder, these machines include MIG welders, TIG welders, Stick welders, and multiprocess welders that can handle various welding methods.
- Consumables: These supplies include electrodes, welding rods, and gases that are burned or consumed during the welding process.
- Protective Gear: Safety gear such as welding helmets, gloves, aprons, and boots are crucial for protecting welders from sparks, heat, and UV rays.
- Work Accessories: This category includes clamps, tacks, and turntables that assist the welder in positioning and securing materials during the welding process.
Importance of Quality Welding Materials
The quality of welding supplies directly influences the integrity and strength of weld joints. Using subpar materials can lead to weak welds, which might fail under stress, causing safety hazards and costly repairs. High-quality materials ensure consistency, reliability, and performance, ultimately leading to successful welding projects. Moreover, investing in premium supplies can enhance efficiency and prolong the lifespan of equipment.
Essential Tools in Welding
Top Welding Tools Every Welder Needs
Every welder must equip themselves with essential tools that aid in producing high-quality welds. Here’s a detailed look at some of these tools:
- Welding Helmets: These helmets protect the welder’s eyes and face from harmful UV and infrared radiation, as well as sparks and spatter.
- Welding Gloves: Specialized gloves made from heat-resistant materials offer both protection and dexterity for the welder.
- Chipping Hammer and Wire Brush: After welding, these tools help clean up the work area by removing slag and spatter.
- C-clamps and Vices: Holding the workpiece in place during the welding process is critical for achieving precision; clamps and vices are ideal for this purpose.
- Angle Grinder: This tool serves multiple functions, including cutting, grinding, and polishing metal components before and after welding.
Understanding Welding Accessories
Beyond the primary tools, a range of accessories enhances the welding process. These include:
- Welding Rod Holders: Essential for managing filler rods while maintaining a focused workflow.
- Welding Magnets: Used to hold pieces together at the desired angle, increasing efficiency in tacking components.
- Slag Rakes: These tools help remove molten metal residues after welding, crucial for preparing surfaces for subsequent operations.
Choosing the Right Equipment for Your Projects
Selecting the appropriate welding supplies and tools depends on multiple factors, including:
- The Type of Welding: Different welding applications require specific machines and accessories; ensure compatibility with techniques like TIG, MIG, or Stick welding.
- Material Being Joined: The type and thickness of materials (steel, aluminum, etc.) dictate the choice of welding equipment.
- Project Requirements: For heavier applications, more robust welding machines may be necessary to guarantee proper penetration and strength.
Safety in Welding
Welding Gear: Protecting Yourself
Safety should be the highest priority in any welding operation. Quality welding gear protects workers from potential hazards associated with welding, including burns, eye damage, and respiratory issues due to inhaling fumes and particles. Essential reflective or flame-resistant clothing, properly fitted gloves, and safety boots minimize the risk of injury.
Understanding Welding Safety Standards
Adhering to safety standards set by organizations such as the Occupational Safety and Health Administration (OSHA) and the American National Standards Institute (ANSI) is vital. These standards specify requirements for safety equipment, ventilation, and workspace organization to protect welders. Compliance with such regulations not only ensures safety but also enhances productivity by minimizing accidents and downtime.
Best Practices for Safe Welding
To maintain a safe welding environment, implement the following best practices:
- Always assess the work area for hazards before beginning a project.
- Utilize proper ventilation to avoid exposure to dangerous fumes.
- Keep fire extinguishers and first-aid kits readily available and staff trained on their use.
- Conduct regular equipment checks to ensure all tools are functioning properly.
- Participate in safety training to remain updated on protocols and practices.
Buying Welding Supplies
Where to Buy Quality Welding Supplies
Locating quality welding supplies begins with identifying reliable suppliers. Online platforms, specialized local stores, and industrial suppliers are vital resources. Online retailers often provide comprehensive product ranges, user reviews, and often better price comparisons, while local suppliers may offer personalized advice and the opportunity to inspect tools before purchase.
Comparing Prices and Brands
When shopping for welding supplies, comparing prices across different brands is essential to ensure value for money. Popular brands like Miller Electric, Lincoln Electric, and ESAB are known for their reliability, but it’s crucial to evaluate what best fits your needs. Look beyond price and consider warranty, customer service, product reviews, and shipping costs when making a decision.
Online vs. Local Welding Supplies: Pros and Cons
Understanding the benefits and downsides of buying locally versus online can help you make informed decisions:
Online Supplies
Pros: Wider selections, often lower prices, convenience, and the ability to read customer reviews.
Cons: Shipping times and costs may vary; you cannot physically inspect the products before purchase.
Local Supplies
Pros: Immediate availability, the ability to seek expert advice, and the chance to form relationships with suppliers.
Cons: Limited stocks might lead to higher overall prices for certain items.
Advanced Welding Techniques
Exploring Advanced Welding Equipment
As welding technology advances, so too do the tools and techniques available to practitioners. Techniques such as Laser Beam Welding (LBW) and Electron Beam Welding (EBW) have emerged as highly advanced methods. These methods provide unparalleled precision and quality, ideal for industries requiring tight tolerances, such as aerospace and automotive manufacturing.
Best Practices for Advanced Welding Techniques
To ensure successful implementation of advanced welding techniques, consider these practices:
- Invest in specialized training to properly understand advanced equipment and processes.
- Regularly maintain and calibrate advanced machines to uphold precise operations.
- Utilize compatible materials that complement the advanced welding techniques for optimal results.
Future Innovations in Welding Supplies
The welding industry is on the verge of numerous innovations focused on improving efficiency, safety, and ease of use. Automation and robotics are increasingly finding roles in welding environments, reducing human labor and increasing precision. New materials and techniques are continually being researched, including advanced alloys and smart welding technologies that adjust settings in real-time for improved performance.