Expert Ice Machine Repair Services to Keep Your Business Running Smoothly
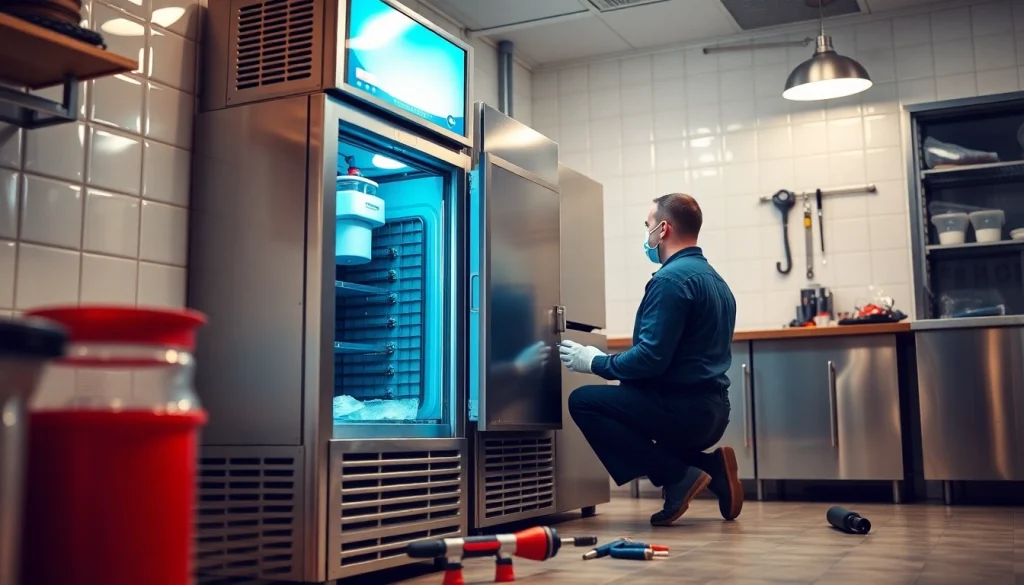
Understanding Ice Machine Repair Needs
Ice machines are essential equipment for many commercial operations, maintaining a steady supply of ice for food preservation, beverage service, and other business needs. When they malfunction, it can adversely affect productivity and customer satisfaction. Therefore, a strong understanding of ice machine repair is crucial for business owners. This comprehensive guide will delve into common issues, troubleshooting steps, and the importance of timely repairs.
Common Issues Faced by Ice Machines
Ice machines can experience a host of problems. Recognizing these can save time and resources. Here are some of the most common issues:
- No Ice Production: This is often the most frustrating problem, with causes ranging from clogged filters to faulty water valves.
- Low Ice Production: Insufficient ice can arise from water supply issues or a malfunctioning compressor.
- Inconsistent Ice Harvest: This issue may indicate problems with the thermostat or the electronic control board.
- Ice Tasting Strange: This can be caused by old water filters or contamination in the water supply.
- Overheating: Ice machines can overheat due to insufficient ventilation, resulting in unit shutdowns.
- Leaking Water: Leaks can occur from various points, including the water supply line or the reservoir.
When to Call for Professional Ice Machine Repair
Determining when to call for professional repair services can be critical for maintaining efficiency. If you notice any of the following signs, it’s advisable to seek expert assistance:
- Persistent issues despite basic troubleshooting efforts.
- Unusual noise or operational irregularities that weren’t present before.
- Ice production stoppage without clear cause.
- Increased energy bills, indicating inefficiency.
- Visible leaks or water pooling around the equipment.
Ignoring these problems can lead to costlier repairs down the line and even significant operational downtime, affecting your bottom line.
DIY Troubleshooting Steps for Ice Makers
Before contacting a repair technician, there are several troubleshooting steps that you can take to potentially resolve issues with your ice machine:
- Check Power Supply: Ensure the unit is plugged in and that circuit breakers are not tripped.
- Examine the Temperature Setting: Verify that temperatures are set correctly according to manufacturer specifications.
- Inspect Water Supply Line: Look for kinks or blockages in the hose that provides water to the machine.
- Clean the Water Filter: A clogged filter can prevent water flow; replace or clean it as needed.
- Check the Timer and Control Settings: Make sure that the control settings are functioning and no fault codes are indicated on the display.
By following these steps, you may resolve minor issues or at least gather useful information for your technician.
Choosing the Right Ice Machine Repair Service
When it comes to ice machine repair, selecting the right technician is as important as knowing what the problems are. The proper service can enhance the longevity of your equipment and ensure efficient operation.
Key Qualities of a Reliable Repair Technician
Identifying a skilled technician requires an understanding of several key qualities:
- Experience: Look for professionals who have a proven track record and experience with your specific type of ice machine.
- Licensing and Insurance: Ensure the technician is licensed for the state you operate in and has appropriate insurance coverage.
- Customer Reviews: Online reviews and testimonials can provide insight into their reliability and quality of work.
- Diagnostic Skills: A competent technician should quickly diagnose issues and provide clear explanations of needed repairs.
- Clear Pricing: Transparency in pricing helps avoid surprises and builds trust.
Comparing Local Ice Machine Repair Services
When facing a broken ice machine, it’s beneficial to research several repair services in your area. Here’s how to effectively compare options:
- Request Quotes: Gather estimates from multiple companies to benchmark pricing.
- Evaluate Service Offerings: Ensure the technician addresses common brands and models of ice machines.
- Check Availability: Some repair services offer emergency support, which can be critical for commercial operations.
- Warranty: Ask if the work comes with a warranty, guaranteeing the quality of repairs.
Understanding Service Fees and Estimates
The costs associated with ice machine repairs can vary widely based on several factors:
- Service Call Fee: Many technicians charge a base fee for assessing the machine, which is typically applied toward the total repair cost.
- Parts and Materials: Replacement parts can significantly increase the cost, depending on the complexity of the repair.
- Labor Costs: Rates can vary based on geographic location and technician expertise. Rough averages range from $75 to $150 per hour.
Being informed about these factors can assist in budgeting for repairs and minimizing unexpected expenses.
Preventive Maintenance for Ice Machines
Just like any other appliance, regular preventive maintenance can extend the useful life of your ice machine and enhance its efficiency.
Essential Maintenance Tasks You Should Follow
Implementing a proactive maintenance schedule can significantly reduce the necessity for repairs:
- Regular Cleaning: Ensure the interior and exterior of the machine are cleaned according to manufacturer guidelines.
- Change Filters: Replace water filters regularly to avoid issues with ice quality and machine performance.
- Inspect Water Lines: Periodically check for kinks or leaks in the water supply lines.
- Monitor Components: Regularly inspect key components, including the compressor, evaporator, and water pump for potential issues.
How Regular Maintenance Reduces Repair Costs
Investing in routine maintenance can substantially decrease repair costs over time:
- Identifying potential issues before they escalate can prevent costly repairs.
- Regularly maintained machines run more efficiently, often leading to lower utility bills.
- Well-maintained ice machines often have a longer lifespan, delaying the need for replacement.
Implementing a Service Schedule for Your Ice Maker
Creating a preventive maintenance schedule is crucial for ensuring your ice machine runs optimally:
- Monthly Tasks: Include filter changes and cleaning routines in a monthly check.
- Seasonal Checks: Conduct thorough inspections at the start of peak seasons.
- Annual Professional Maintenance: Schedule an annual check-up with a professional technician to conduct a comprehensive assessment.
What to Expect During an Ice Machine Repair
Understanding the repair process can help ease concerns and ensure you’re prepared for any eventuality during a service call.
Step-by-Step Process of Repair Services
Here’s what typically happens during an ice machine repair:
- Initial Assessment: The technician will evaluate the machine and identify the problem.
- Explanation of Issues: After diagnosing, the technician will explain the issues and possible solutions.
- Parts Replacement: If necessary, they will proceed with replacing faulty parts.
- Testing: Post-repair, the technician will test the ice machine to ensure proper functionality.
- Final Review: They’ll provide guidance on keeping your machine in ideal working condition.
How Long Do Ice Machine Repairs Typically Take?
The duration of repairs can vary based on the complexity and required parts:
- Simple Repairs: Such as parts cleaning or filter changes may take an hour or less.
- Intermediate Repairs: May take several hours, especially if parts must be ordered.
- Complex Repairs: Involving major component replacements can take a day or more, particularly if special parts are needed.
Evaluating Parts Replacement vs. Repair
One crucial question that often arises during the repair process is whether to repair a part or replace it entirely. Consider these points:
- Cost of Repair vs. Replacement: If repair costs are nearing or exceeding the price of a new part, replacement may be the most logical choice.
- Lifespan: New components can extend the overall lifespan of the machine.
- Manufacturer Recommendations: Follow manufacturer guidance on which parts are best replaced after certain periods of use.
Cost Factors in Ice Machine Repair
Understanding the factors that determine repair costs can help you prepare financially and make informed decisions.
Average Costs for Common Ice Machine Repairs
Here are some common repairs and their associated costs:
- Replacement of a Water Filter: Approximately $30 to $100.
- Cleaning Services: Usually around $100 to $300, depending on the complexity.
- Compressor Replacement: This can range from $500 to $1,500, based on brand and type.
- Control Board Replacement: Typically costs between $200 to $800.
Understanding Labor Costs vs. Parts Costs
Every repair will entail both parts and labor. Understanding how this breakdown works can help manage your expectations:
- Parts Cost: This is typically one-time and can vary widely depending on brand and availability.
- Labor Cost: Hourly rates for technicians can vary based on their experience, location, and market rates.
How to Prepare for Unexpected Repair Expenses
Every business should be prepared for the possibility of unexpected repair expenses:
- Budget for Repairs: Set aside a maintenance fund to cover potential costs throughout the year.
- Identify Repair Insurance: Some businesses choose to invest in repair insurance options.
- Keep an Emergency Contact List: Have a list of trusted repair technicians on hand in case of emergencies.
Understanding ice machine repair, knowing when to seek help, and investing in preventive maintenance can not only enhance your operational efficiency but also extend the life of your investment. By following these guidelines, you can ensure your ice machine is always ready to serve your business needs.